Healthcare has long been Layton’s bread and butter. With a team of experts who’ve dedicated their careers to meeting patient and staff needs, we continue to set the standard for how these facilities should be built—no matter the size or complexity. Our commitment to quality and care is immanent in every project we take on, and it’s been exemplified in our approach on St. Luke’s Boise Medical Center in Idaho.
As a multi-phase build, the extensive project at St. Luke’s Health System’s flagship campus includes a variety of new and renovated facilities. Approved by the city of Boise in 2015, the hospital’s master plan started with a new children’s pavilion to support St. Luke’s Children’s Hospital, the only children’s hospital in the state.
The next phase of the master plan, led by Layton, included a parking garage, a shipping and receiving building designed and constructed to reduce the impact on surrounding neighbors, and a central utility plant (CUP) that significantly improved the medical center’s operations. Following the demolition of the outdated CUP, the next phase includes a new hospital tower and medical office plaza. Within these efforts, our team has also completed major utility work and preservation of historic buildings in the area—which is nearly a project in itself.
Coordinating Utilities: More than Flipping a Switch
Part of St. Luke’s mission to improve the health of the surrounding communities includes enhancing access to healthcare services for patients—something Layton can always get behind. This led to the development of a parking garage near State Street, a major roadway in Boise. The Layton team guided the construction of the garage, which is attached to the new energy-efficient central utility plant. The parking garage is eight levels with two below grade and has nearly 1,100 stalls, while the new utility plant meets all the needs for the ongoing hospital campus expansion.
For reference, the St. Luke’s campus is a conglomerate of buildings constructed over the past 100 years, and many of the older utilities needed to be upgraded. The existing CUP was one of them, but it fed the boilers and chillers for the existing hospital. With this, none of these could be turned off.
“We had to finish this part of the build and then run all the piping, steam piping, chilled water piping, and emergency power to the existing hospital and essentially switch over to the brand-new CUP to take the old CUP offline,” says Jeremy Hobbs, vice president at Layton Construction. While flipping a switch sounds simple, the process was more complicated. “Most of the coordination and complication came with this part of the project,” Hobbs adds.
Though this work above ground was extensive, the project also required going underground.
Navigating a Geothermal Line to Install Underground Infrastructure
Though this work above ground was extensive, our project team also had to go underground, adding infrastructure to support the hospital’s operations. The team led an extensive shoring effort and deftly maneuvered around the city of Boise’s underground geothermal line. The city disconnected the line and, when construction finished, reestablished the geothermal component.
“We had a temp geothermal line tied in supported by steel structure, so that we could go underneath that geothermal line,” Hobbs says. “It was extensive.”
While these issues required us to think carefully about the build process, nothing was as complicated as the crossover of the new utilities with the old. Once the new utility plant was finished and all the lines were built in the tunnels, our team had to determine how to change them over.
“The challenges with this are if there isn’t a load on the boilers and chillers, it’s hard to get through the commissioning process,” says Hobbs. “We had to have 100% confidence that the boiler is absolutely going to provide steam to the building when needed.”
Typically, when building a CUP on a new project, the team tests everything with load; however, with an operating hospital, that wasn’t possible. “We needed to simulate them,” Hobbs says. “These steam lines came from the existing utility plant, so in the summer we went in and shut down the steam and installed the valves. We only had a certain amount of time to get those installed.”
Time was limited, as if the steam temperature drops too low, the gaskets can begin to fail and cause leaks. With this small window, they went through “iterations upon iterations” to make sure there were no mistakes before starting the process. Ultimately, all the work to get things set up ended with a simple flip of a switch. But our team wasn’t done there.
Import/Export
Alongside the parking garage and CUP, the Layton team completed a second building for shipping and receiving, which serves as a hub for a unique pneumatic tube system that connects to the existing hospital. When hospital workers need to send trash or linens to the new building, they must walk through the underground connection about halfway; then the trans-vac system does the rest. On the opposite side, when products arrive by semi-truck, they are unloaded and brought to a large freight elevator before being distributed to support the medical center.
Finally—for this phase of the project at least—our team also installed a brand-new medical gas farm, emergency generators, and paralleling gear on the roof, meeting the operational needs of the hospital.
Moving Forward
Layton continues to push forward in bringing this massive project to completion, with heavy preconstruction efforts for the next phase well underway. As the larger chapter of the master plan phases, it will provide Boise and the surrounding communities with improved access to healthcare and updated medical facilities.
See Layton’s Healthcare portfolio.
About Layton Construction
Layton Construction is a privately held national general contractor, delivering predictable outcomes in commercial construction since 1953. Headquartered in Salt Lake City, Utah, Layton operates from 16 strategic offices across the United States, employing more than 1,400 construction professionals who serve diverse markets including healthcare, education, commercial office, industrial, hospitality, and multi-unit residential. Founded on the core values of honesty, unity, safety, and quality, Layton has built a reputation for excellence in complex project delivery while maintaining strong partnerships with clients, architects, and trade partners nationwide.
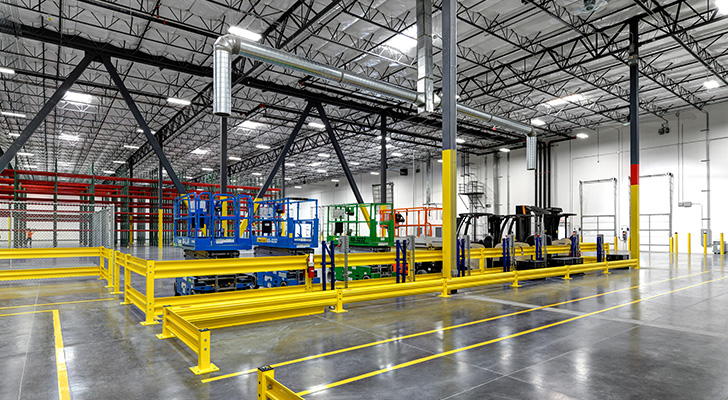
Considering the complexities of cold storage facilities, their construction demands a specialized approach and expertise. And with such a rapidly growing market, key players like Layton are primed and poised to step up.
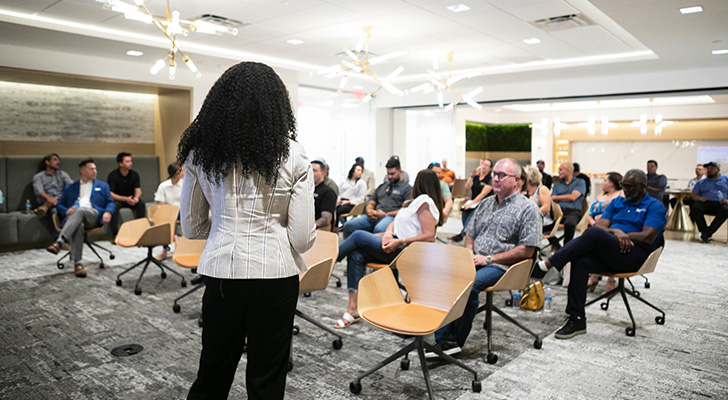
Layton depends heavily on the expertise and capabilities of our trade partners. Lead by Cherelle Cortez, our Trade Partner Engagement and Development team is focused on increasing the diversity and strength of our trade partners.