When Hurricane Ian struck Florida in September 2022, the impact was devastating. Buildings and homes were destroyed; communities lost power; and hospital patients throughout the state were forced to relocate. One such hospital—and a long-time Layton client—is accustomed to dealing with storms, and they knew what was coming.
Acting on tremendous foresight, our client decided to get ahead of the impending damage and asked Layton to lead the eventual cleanup and rebuilding efforts. Without hesitation, our Florida-based team answered the call—stepping in and stepping up.
Ready and Waiting
Preparation efforts commenced immediately as we listened to our client’s needs. In the two weeks leading up to the storm, Construction Manager Jim Parker—who’s no stranger to hurricane remediation—led the charge, getting in touch with construction managers, contractors, and trade partners while making calls to place generators. “I’m usually driving to the hurricane every time. Irma and Michael—I’ve been privileged to help with these areas, so I know what’s going on,” he remarks. Ultimately, with Jim at the helm, we had all the resources set aside to come in and hit it hard. From MEP to drywall, everyone was at the ready.
By the time Ian made landfall, the hospital evacuation was well under way. Light poles were knocked down so helicopters could land; hundreds of ambulances lined the surrounding blocks. In just a matter of time, all 150+ patients and hospital staff were completely evacuated. Amidst the chaos, Layton and crews were standing by. Just one day after the storm, our teams had boots on the soggy ground, getting straight to the cleanup. From there, crews moved in and assessed the damage—which was nothing short of extensive.
Though the 250,000 SF building withstood the storm and kept patients and staff safe inside, it suffered significant roof, equipment, and water damage. As crews continued the cleanup efforts outside—clearing the lots and picking up canopies that had been ripped down by the storm—others set their sights on the rebuild . What would that entail?
High Impact at Higher Ground
For starters, debris had hit the side of the hospital hard, gouging the wall and allowing air and water in. A rogue 2×4 flying through 120+ MPH winds is akin to a missile, wreaking havoc wherever it hits . In our case, it dislodged the parapet and pulled the roof material back about 200 feet, while busting a six-inch storz (fire hydrant connection). Along with torrential rain from the storm, water flowed from that pipe for 28 hours straight, continually flooding the building. But things quickly worsened. Not only was the roof compromised, it wasn’t draining. The weight of the gathering water began to pose a threat to the building’s structural integrity. Acting quickly, our team opened elevator shafts, stairwells, and roof access to let the building drain.
As with any flood, once the water stops flowing, new challenges emerge. The hospital’s building materials were vulnerable to dangerous amounts of water damage—a profoundly serious condition for an operating facility. Though the Layton team accounted for this in our initial plan, proper execution felt critical—there was no room for error. “First thing’s first: you need to get the water out of the building and start demoing everything that’s wet,” Parker explains, “… and that’s where the abatement process comes in.” What’s typically a simple remediation job was complicated by the post-storm pressure to ensure all potentially contaminated materials were removed. It’s painstaking work and the team moved foot by foot to assess, remove, and replace the drywall and other materials.
As for the work environment? “Absolute chaos—organized chaos,” says Jim Parker.
Keep in mind, up until the storm, this was an operating hospital. In the aftermath of the Category 4 hurricane, upwards of 350 people were on site daily plugging through the aftermath and navigating around the chairs, beds, IV poles, and various equipment still in the building. As Layton’s crews came in to start the work, they had to get the equipment out—demobilizing the facility and filling conex containers to the brim. While this was certainly something to work around, it was far from the only issue the teams faced.
Riding Out a Storm of Challenges
Though the remediation required was a serious undertaking in itself, the project presented several additional challenges along the way. At this time, the construction industry was facing significant labor and material shortages with incredibly long lead times. Crucial elements like roofing were hard to get; HVAC ducting was hard to get; and casework was extremely hard to get. We relied heavily on our trade partners to secure the necessary components. Did they ever come through! Skyler Design Build marshalled its resources and brought significant manpower to the job. Miller Electric worked around the clock from the moment they arrived on site to restore power after running on generators for nearly a week. Their team went through the entire building, exhaustively checking every breaker and circuit, literally.
Unforeseen issues continued to mount, but somehow help always came. When our original casework supplier couldn’t deliver on their commitment, a company out of Canada mobilized and brought down the necessary materials for the last phase, without skipping a beat. The help didn’t stop there. We had vendors from South Carolina come with 18-wheelers packed with supplies. Companies from Tampa dropped off equipment at all hours. We couldn’t get dumpsters locally, so a company from Texas showed up with 26 of them. It was clear: there are some great people out there willing to help those who need it most.
“These things are out of this world amazing.”
Layton stayed in problem solving-mode as other barriers presented themselves. Some owner furnished equipment wasn’t ordered, so we had someone fly to Nashville to pick up ice machines while we scoured the entire state of Florida to find paper towel and toilet paper dispensers. Next came the roofing—tough material to acquire under normal circumstances. Never losing momentum, we went straight to the manufacturer and pulled the roofing material right off the production line.
The only thing that changed more than working conditions were the new teams coming on and off the site to help. Because of the nature of the work and the urgency of the schedule—sometimes requiring a 24/7 effort—handoff from crew to crew was constant. Naturally, new teams would need clarity about the scope; however, it was never cut and dried. Conditions changed constantly as each day passed and more moisture moved through the building. And did we mention that all this work took place during the holidays? We will be forever grateful for the time crews sacrificed with their loved ones to show up and help in this emergency situation.
When Mother Nature Hits, Layton Hits Back
While hurricanes are certainly a force to be reckoned with, through this experience it became clear that Layton and the teams we work with are too. Given the nature of the project, the rewarding work, and the relationships Layton built, we continue to feel surprised by all that we gained in this effort. The weather was hot; the holidays came and went; and this team withstood it all to get things done. For Jim Parker, it’s just being human. “When you see the devastation of the whole community, you have to think, ‘we need to build this hospital back. They need this,’” he says. “Without everyone’s commitment, it wouldn’t have happened.”
It did happen, though, and we thank each and every Layton employee and company for all their efforts on such a meaningful and important project.
- ABG Caulking
- Atlantic Roofing and Waterproofing
- Bonitz, Inc.
- Carmack’s Quality Aluminum
- Johnson Controls, Inc.
- Johnson & Sons Plastering
- KHS&S
- Miller Electric Company
- Skyler Design Build
- RJ Wherry & Associates
- Alliance Fire & Safety
- Old Dominion Firestopping
- Trident Construction
- Trifecta Services
- W.W. Gay Mechanical Contractors
See Layton’s Healthcare portfolio.
About Layton Construction
Layton Construction is a privately held national general contractor, delivering predictable outcomes in commercial construction since 1953. Headquartered in Salt Lake City, Utah, Layton operates from 16 strategic offices across the United States, employing more than 1,400 construction professionals who serve diverse markets including healthcare, education, commercial office, industrial, hospitality, and multi-unit residential. Founded on the core values of honesty, unity, safety, and quality, Layton has built a reputation for excellence in complex project delivery while maintaining strong partnerships with clients, architects, and trade partners nationwide.
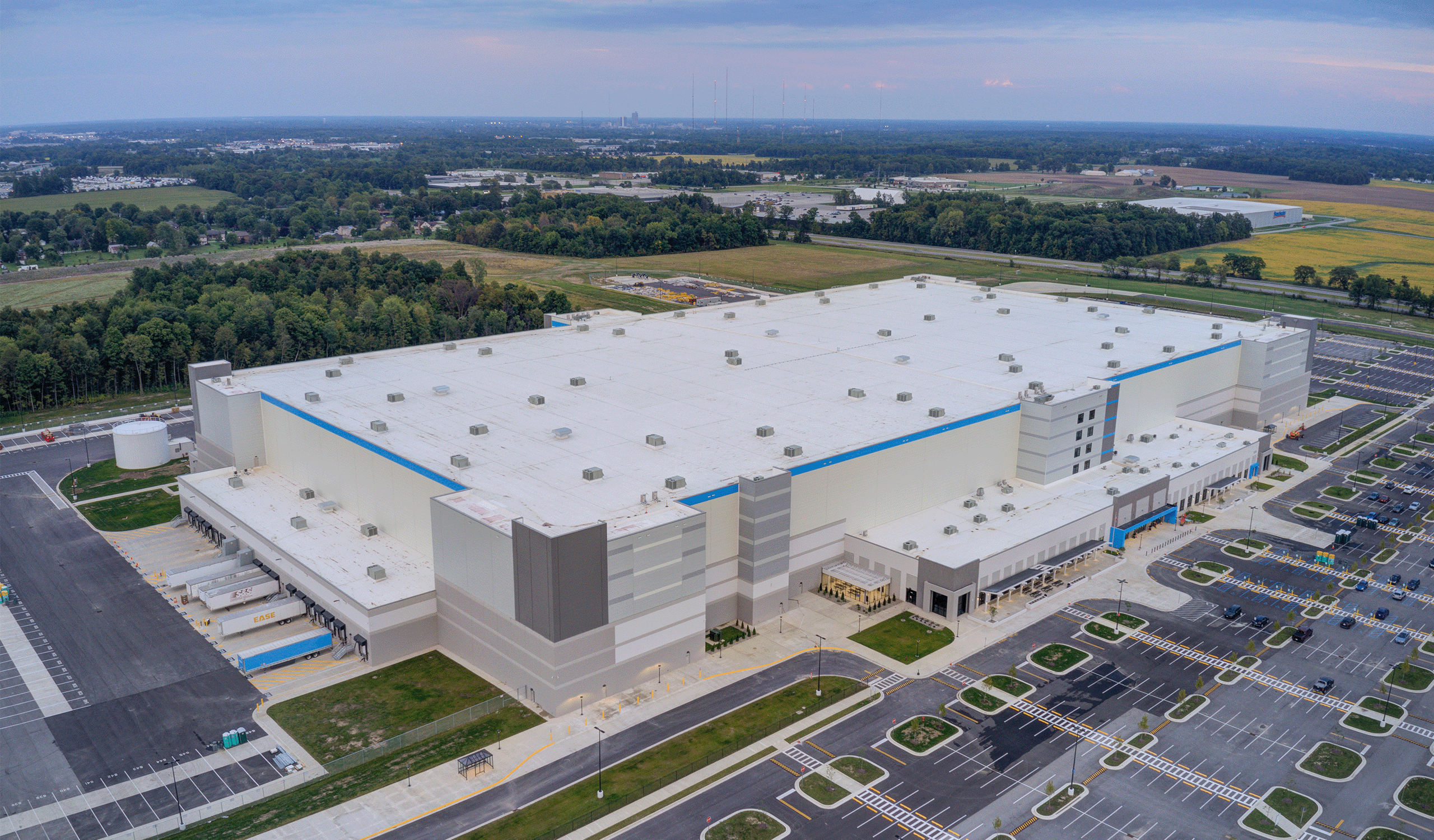
Layton is committed to being a wise steward of the environment by continually seeking ways to reduce our impact and build sustainable facilities.
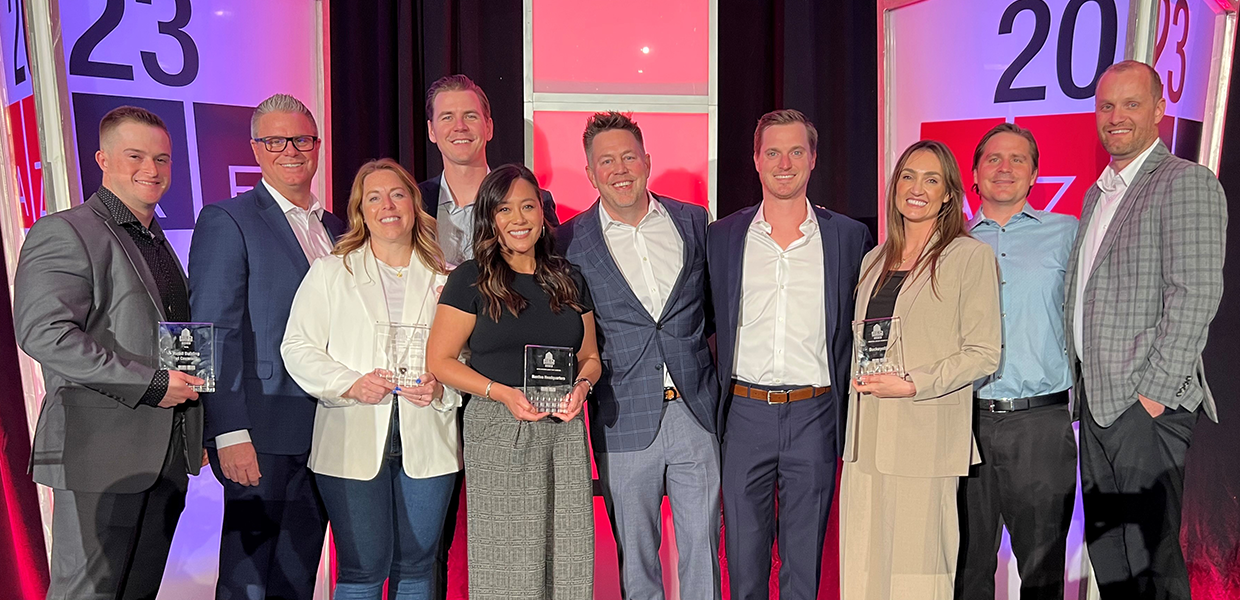
Layton strives to go the extra mile to ensure everything we put our name on says “best in class.” We’re proud of the work we do, and we’re grateful to be recognized as leaders in our industry.