In today’s dynamic business landscape, where schedules and profitability drive nearly everything, talk of company values may take a back seat, especially in times of stress. “Layton Construction’s values aren’t just a compass, they’re our anchor, and maintaining them is a strategic imperative,” says our president and CEO, David S. Layton. What are the Layton values and how do they guide and shape our culture, decision-making processes, and overall identity? We’re glad you asked.
Roots of Resilience: The Beginnings of Layton’s Values
In February 1953, our founder Alan W. Layton took a giant leap of faith. With a new mortgage, five small children, and just $1,600, Alan left a secure government job and hired two retired neighbors to start Layton Construction’s very first project. Back then, there were no written contracts, cost reports, or progress reviews. Just hard work, long days, and the hope there’d be a little money left after they finished the job.
A decorated WWII veteran and model of America’s “greatest generation,” Alan’s vision for Layton was simple: commit to constructing with integrity through honesty, unity, safety, and quality. Shortly after his retirement, he sent a letter to his sons where he offered sage management advice and counsel, and reemphasized the same principles that helped found his beloved construction company. Seventy years and over 3,000 projects later, these values have been canonized and continue to guide the entire organization.
Layton fervently follows Alan’s counsel today, striving to let honesty, unity, safety, and quality drive everything we do. With our modest beginnings in mind, we share the following project stories that illustrate our commitment to our founder’s vision and respect for his legacy.
Honesty: Hiking Up-Hill with Cost Escalation
When Layton partnered with Seattle-based Abbott Construction in 2019 to build Mary Bridge Children’s Hospital in Tacoma, few, if any, could’ve imagined the distinct challenges awaiting the joint venture team.
To build a facility best suited for children’s healthcare, and one that maintained the client’s objectives, the Layton-Abbott preconstruction team would utilize Lean design principles and integrated project delivery (IPD). These methods—employed to improve efficiency, reduce waste, and increase productivity—demand total collaboration and trust among everyone involved in a project.
Since the 300,000 SF hospital will provide a variety of dedicated pediatric healthcare services—all of which are crucially needed in the region—the various parties involved were motivated to work together to fulfill the client’s objectives. But the impending impacts of a worldwide pandemic would test the entire team’s resolve.
Mary Bridge Children’s Hospital will have 82 private patient rooms, 10 ORs, a PICU, a hybrid interventional cardiology and radiology suite with dedicated MRI, CT, and ultrasound, a state-of-the-art infusion center, endoscopy, lab, pediatric emergency department with 38 treatment rooms, pharmacy services, and pediatric mental health crisis stabilization—all with shelled space to meet future needs.
Laying our Cards on the Table
Preconstruction began on the eve of historic cost escalation. As the global supply chain collapsed and government restrictions tightened, construction material and labor costs soared to the tune of 40-50%. Seemingly overnight, the original design was significantly over budget. Still, the project team remained determined and connected.
“We knew getting this project back on track would be tough,” recalls Trent Isaacson, Layton’s vice president of preconstruction. “We were upfront about it. We didn’t paint a picture that we can get all this done. We told them we’re hiking uphill.”
Dividing, Conquering, and Rolling up our Sleeves
The IPD team quickly established a plan to review the entire project and fine-tune the details. In a series of component team meetings—comprising designers, stakeholders, trade partners, owner representatives, and builders—assigned participants focused on specific elements of the project to identify efficiencies and opportunities for cost savings. Through it all, the Layton-Abbott team maintained an honest dialogue with the client. They developed executive-level dashboards, offering up-to-the-minute budget status even as components and costs continued to change. In the end, they were able to identify significant cost savings as a team, all without compromising the project goals.
“We laid all our cards on the table,” Isaacson said, “giving them the information they needed to make confident decisions.”
Mary Bridge Children’s Hospital
The Best Policy
Ultimately, some changes were made, and the project ended up below budget. Yet, as construction began in 2023, even Isaacson was in disbelief seeing the favorable outcome despite the challenges they’d overcome.
“We’re still providing them what they wanted,” he said. “They’re still getting the same number of beds and their base program remains the same. If it wasn’t for that honest, open, transparent dialogue—them trusting us and believing what we were telling them—we never would’ve gotten there.”
Unity: Planning Down to the Hour
On a warm Friday evening in July 2022, Layton began the arduous task of pouring nearly 4,000 cubic yards of concrete for the foundation of a 31-story residential tower in Salt Lake City. The continuous, 8,000-ton pour took 414 trucks, dozens of Layton employees and trade partners, and just 11 hours to offload and finish. Neighbors and news media even showed up to watch the team carry out this historic mega-pour.
Nearly 30 years earlier, Layton’s concrete crew had set a company record by continuously placing 1,500 cubic yards of concrete in 20 hours. How did our residential tower team pour nearly three times as much concrete in almost half the time? The answer has been the same for 30 years. “None of this happens unless every member of the team is united in achieving our shared goal,” said Patrick Taylor, one of Layton’s superintendents over the project.
In the months leading up to the pour, every procedure was planned down to the hour—convening with trade partners, concrete suppliers, and pump truck operators to mitigate any possible bottleneck. All tradespeople focused on closing out their scope, laborers ensured the site was cleared of all obstacles, and extra Layton staff were brought in to assist with the coordination.
The Layton team completed the foundation pour with few issues, setting a precedent for collaboration that would drive the success of each remaining pour and eventually get this concrete tower topped out. “Precise planning and clear communication—and the entire team’s willingness to execute—delivered a predictable outcome,” said Taylor, adding, “this is the Layton way. It is our foundation.”
“Employ quality employees and work with skilled subcontractors.” – Alan W. Layton
Safety: A Tall Order on a Tight Site
Each year, Layton bestows the Oak Hard Hat Safety Award upon the project team that exhibits exemplary dedication to safety, particularly on a complex project. In 2022, this accolade was earned by the Wilcox Medical Center Emergency Generator System Replacement project team in Lihue, Hawaii, for their outstanding safety record against formidable challenges.
Outwardly, this project seemed straight-forward: expand an existing central utility plant (CUP) and replace a few generators. However, several variables elevated the complexity and presented unique hurdles in maintaining safety at each stage.
Wilcox Medical Center is Kauai’s only Level III trauma center, so the entire project had to be completed without interrupting round-the-clock hospital operations. Construction also commenced in March 2020 at the height of the island’s rainy season and amidst a global pandemic, requiring the team’s strict adherence to local, hospital, and Layton’s own COVID-19 protocols.
Operationally, sequencing and staging were far from straightforward. The existing space wasn’t large enough to accommodate the new generators, necessitating the construction of a 40-foot-tall second level atop the existing and fully operational CUP. Intricacies increased as we accounted for the surrounding obstacles—an active delivery driveway to the west, chillers on the south, power lines to the north, and water and fuel storage tanks to the east.
To successfully navigate around this congestion, Layton would need to perform more than 95% of the work from scaffolding on grated flooring, 20 feet above grade. And once the vertical expansion was complete, we’d then need to hoist three 20,000-pound generators (and all supporting equipment) through relatively small penthouses on the roof.
The final hurdle? Switching over a live electrical load from the old generators to the new ones, all without disrupting power to the 24/7 emergency room.
There’s a Plan for [all of] That
How does a project team overcome unique challenges and manage a project with zero safety incidents? Meticulous planning, constant communication, precise coordination, and of course, establishing a culture of safety at the project’s outset.
From the beginning, the Layton team focused on aligning all parties on our safety protocols and the need for strict adherence from the client and trade partners alike. “We conveyed the importance of looking out for everyone on campus, including those who could be walking or driving by,” said Layton Project Manager Ashley Quinn. “Every individual was responsible for the safety of others.”
Pre-mobilization meetings offered continuous training on Layton’s Safety 360 program. Thorough pre-task plans and daily huddles fostered unity among all involved. Each construction activity was planned, discussed, and coordinated, and the details relayed to all stakeholders.
Incredibly, after nearly 75,000 worker hours, the Layton team completed the project entirely accident free while maintaining the original schedule and budget. That’s “good business.”
Quality: The Fastest Ice on Earth
The 2002 Winter Olympic Games brought athletes and spectators from around the world to Salt Lake City, giving Utah a chance to step onto the global stage and showcase its natural beauty and the community’s culture and hospitality. With the need for so many venues, the Olympics were also an opportunity for us to demonstrate our skill in constructing several of those venues, including the Utah Olympic Oval, home to the speed-skating events. Building a 400-meter-long track and two ice rinks to international competitive standards demanded unwavering attention to detail and rigorous quality control. Like the athletes who’d compete on the ice, the Layton team proved they were up to the task.
The Need for Olympic Speed
What makes the ice sparkle on top for world-class speed skaters is largely determined by what is meticulously placed below and within the concrete slab.
To get a world-class-level ice sheet, a gravel base is topped with sand and hot-water-filled heat tubes placed within the sand layer. Four inches of rigid foam insulation covered with plastic sheeting (which serves as a vapor barrier) provides a stable base upon which the reinforcing steel, refrigeration lines, and concrete are placed.
Pouring Over the Details
After months of planning and weeks of intricate placement of insulation, reinforcing steel, and 33 miles of refrigeration tubing, the Layton team began pouring nearly 1,000 cubic yards of concrete. The team used a state-of-the-art laser screed to control accuracy, while crews worked 12 straight hours to complete the seamless five-inch-thick slab.
The lengthy curing process then began. A 14-day “wet cure” helped ensure a slow dehydration of the concrete to prevent cracking. Construction officials and skaters waited patiently through another 30-day “dry cure.” The superflat surface was then polished to near-marble smoothness.
At last, the concrete was then ready for ice. A chilled brine solution flowed through the refrigeration system to lower the temperature of the concrete at a rate of three degrees Fahrenheit per day. When the concrete reached the temperature of 18°, water was put down on the concrete surface in several applications, creating a nearly two-inch layer of ice. The process took 10 days to complete.
The Utah Olympic Oval is a 267,000 SF facility completed for the 2002 Salt Lake Olympics. It was also the first LEED certified project in Utah.
The Test of Time
Ten Olympic records and nine world records were set at the Oval during the 2002 games, the most ever set at one event. More than two decades later, four of the Olympic records still stand, and another 25 world records have been set at the Oval, earning it the honor of Fastest Ice on Earth. The Oval truly stands as a symbol of Layton’s quality and first-class craftsmanship long after they’ve left the jobsite.
The Layton Way
With people spread across 12 offices, it’s imperative that our staff represents Layton’s values no matter where they’re encountered. From our humble beginnings and throughout our history, Layton has set out to construct with integrity, provide predictable outcomes, and embody the core values that have been our foundation for 70 years. The principles of honesty, unity, safety, and quality have had a profound impact on our culture, relationships, and our overall growth, and we look forward to forging ahead and continuing to let these values propel us into the future.
About Layton Construction
Layton Construction is a privately held national general contractor, delivering predictable outcomes in commercial construction since 1953. Headquartered in Salt Lake City, Utah, Layton operates from 16 strategic offices across the United States, employing more than 1,400 construction professionals who serve diverse markets including healthcare, education, commercial office, industrial, hospitality, and multi-unit residential. Founded on the core values of honesty, unity, safety, and quality, Layton has built a reputation for excellence in complex project delivery while maintaining strong partnerships with clients, architects, and trade partners nationwide.
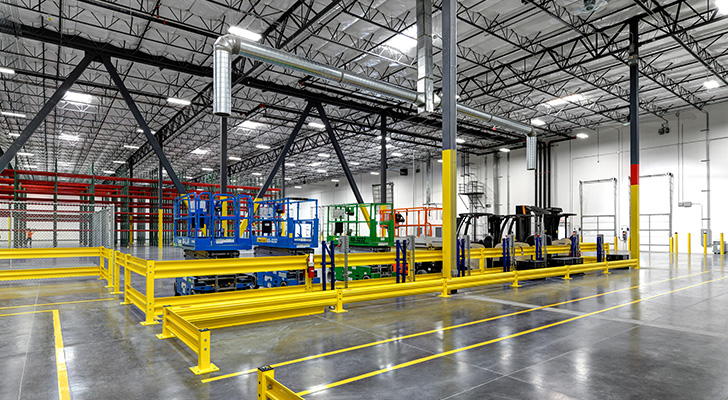
Considering the complexities of cold storage facilities, their construction demands a specialized approach and expertise. And with such a rapidly growing market, key players like Layton are primed and poised to step up.
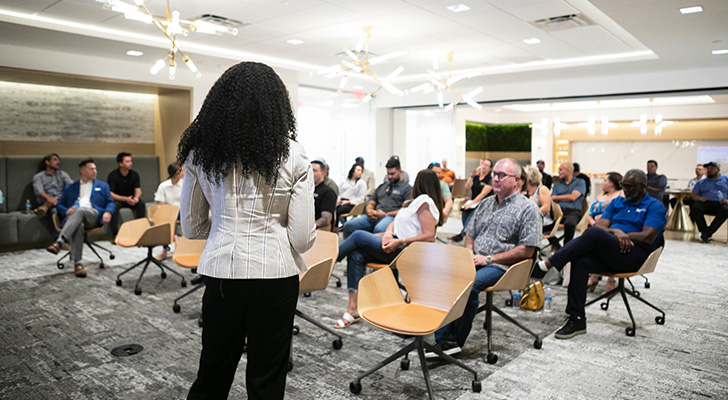
Layton depends heavily on the expertise and capabilities of our trade partners. Lead by Cherelle Cortez, our Trade Partner Engagement and Development team is focused on increasing the diversity and strength of our trade partners.