The golden age of Hollywood may be behind us, but the demand for captivating content is higher than ever. A production boom is spreading across the west, driven by established production giants like Warner Bros. and Sony Pictures, mega streaming platforms like Amazon Studios and Hulu, and indie outfits popping up constantly. A critical reality is now making itself known: There’s not enough specialized, physical studio space to keep up with it all.
Hubs of Concentrated and Unique Activity
They cater to an array of production and operational needs with spaces for filming, sound recording, editing, craft services, star wagons, backlot storage, and more. With that, they not only demand an intimate understanding of how a production house operates, but their varied uses require sophisticated planning and foresight so the final product meets the various needs of the end-users.
Layton boasts a cast of construction veterans who’ve overseen a range of studio projects throughout their careers—experience that goes beyond building type and name recognition, though it’s worth mentioning they’ve built for industry titans like Netflix, Disney, and Universal Studios (to name a few). Not only do they recognize the intricate interplay between soundproofing, power distribution, and material selection, for example, but they’ve also tackled projects in diverse sectors—including industrial, where means and methods surprisingly complement the needs of building in the production world.
A conversation with our California market and studio building experts revealed valuable insights on current market conditions and trends. Whether you’re a studio executive or recent college graduate looking to get started in construction, we think you’ll like this one.
Source: “Physical Production Studio Trends”, Deloitte
Finding Neverland: Build New or Repurpose?
One of the first decisions facing developers in any studio project is whether to repurpose an existing building or construct a studio from the ground up. This decision can be particularly challenging in cities like Los Angeles. Limited available real estate and strict regulations from acting unions—such as commute times and per diem requirements—complicate the decision-making process. Los Angeles’ Arts District, for example, is rife with large, available industrial spaces ready to be repurposed. In fact, Layton broke ground on East End Studio’s Mission Campus there in July 2024—converting a vacant cold storage warehouse into soundstages, offices, production support, and more. But because these spaces come with extensive rework, permitting challenges, and other hurdles, developers are increasingly seeking opportunities to build new in more remote places in the west.
Layton is currently under construction on the Mission Campus for East End Studios in the Los Angeles Arts District. Renderings courtesy of Relativity Architects.
Details of a Studio: The Usual Suspects
Regardless of building type and location, there’s much to account for when working in this vertical. Along with managing the actual construction process, we’re mindful of what’s important to studio executives, producers, labor unions, regulatory agencies, and even neighboring communities.
The film, television, and music industries are highly competitive, with tight production windows and fixed budgets. And despite high demand for their product, the entertainment world is not immune to the impact of economic conditions. The sooner a studio is operational, the sooner it can capitalize on revenue-generating opportunities and recoup investment costs.
Whether building something from the ground up or converting an existing facility into a premier studio space, “the number one concern for these clients right now is interest carry,” explains Thomas Smith, Layton California Vice President. He continues, “With interest rates peaking upwards of 7%, clients want to get rid of those loans as fast as possible.” That said, two major elements come into play…
On a typical project, cost management and speed to market can be attained through an effective preconstruction process. But with studio work, Layton takes a multi-faceted approach. We analyze the structural system, material selection, technical infrastructure, space optimization, and sustainability. And Smith emphasizes futureproofing and asking the right questions: “These developers need a contractor that understands the need for flexibility based on tenant demands. These spaces need to be adaptable, but they also have to hit the price point.” He adds, “They’re different from retail or multifamily where you’re building what’s on paper. With studios, there are adjustments; what’s the site look like? If we’re retrofitting, what walls can stay or go? It all depends on the client.”
In essence, sometimes seemingly minute details require the entire team’s attention. Others demand some foresight.
Beam me up, Scotty! Assessing the Structure
Considering the increasingly limited real estate in Los Angeles, adaptive re-use and retrofitting are on the rise. Most existing structures can’t accommodate the heavy loads of production equipment, so reinforcing the structural system becomes paramount. But this is hardly ever simple. “With a retrofit, how you approach maintaining the existing structure or attaching to another can get very technical,” says Smith.
Layton Sr. Project Manager Dan Condreay—whose tenure in the field has given him an instinct for what works best on a project with limited accessibility and laydown space—refers to the sequencing process as putting a puzzle together, or better yet, “assembling a paper doll.” He explains, “Let’s say you’re working with a barrel roof on a wood truss building with irregular, arched panels. We’d use an old school approach to shore up the existing building and then cut out panels on a scale model to determine the best way to fit the reinforced elements on the slab. And we do this as fast as possible to keep the project moving.”
Smith adds, “Having an understanding of how these projects come together and the necessary engineered shoring systems is crucial—that’s where our expertise shines. We’ve dealt with zero laydown on a range of projects. And we’ve done it all right here in LA.”
More importantly, the speed that comes with this experience proves paramount to studio clients—where time (and cost) is always of the essence. “We’ve done so many of these [retrofits], we know how to flip the buildings on a tight footprint in a congested area—and we know how to do it fast.” Smith continues, “We’re leaving certain walls up to expedite the entitlement process. The permitting process then goes faster, and the studio is up and running sooner.”
Layton’s Southern California team is made up of construction experts who’ve built for some of the largest production companies in the industry.
A Sixth Sense for Building Materials and Techniques
From a technical perspective, several factors set production spaces apart from typical commercial builds, and we account for all of them. Number one?
“Sound is everything when you’re building a studio,” says Condrey.
He continues, “A plane flies overhead, a car drives by, sirens in the distance—nothing can disrupt the filming.” Most buildings take insulation and soundproofing into account during material selection, but studios and sound stages depend heavily on meticulous noise reduction and sound control to ensure pristine audio. Studios are frequently set in urban areas where noise pollution is a near constant. Unfortunately, the overall design of these facilities doesn’t always account for strict soundproofing. Condrey adds, “No matter what the architect draws, you need to make sure the structure completely isolates the interior.”
Of course, Layton prefers to get involved on all projects during the design phase to ensure everything drawn is buildable. But in the case of studio work, our early involvement becomes even more pressing. We account for material selection specifically to ensure all walls, ceilings, and floors are designed to achieve optimal sound isolation. Additionally, the acoustical properties of the materials used throughout a soundstage heavily affect the overall soundproofing quality, so we’re mindful of those too.
The Sound of Silence
When it comes to structural options, keeping the outside noise outside is just one consideration. Beyond the initial design, material selection plays a crucial role in achieving optimal sound quality within the studio walls, and we’re constantly looking to strike a balance between schedule, cost, function, and quality with all options.
Concrete tilt panels, for example, offer a compelling combination: fast erection, durability, and inherent noise reduction. This makes them a strong contender for studios requiring robust sound isolation. But tight sites or retrofits don’t always have the required laydown space for tilt panels.
Traditional steel trusses, while common for their load-bearing capabilities and availability, can be problematic for sound studios. They can create unwanted reverberation and have a higher carbon footprint, which may not align with a client’s sustainability goals. Thankfully, advancements in sustainable building practices offer exciting alternatives. Mass timber, for instance, boasts excellent acoustic properties and lower environmental impact.
Every project has unique needs, and every potential issue tied to material selection likely has a solution. Layton’s expertise lies in navigating these considerations during preconstruction . We work closely with clients to identify the most cost-effective and acoustically suitable materials for their specific needs.
We’re Gonna Need a Bigger…Door
Imagine a door so big even an elephant could squeeze through. That’s the essential function of elephant doors in a studio. These sliding doors allow massive sets and equipment to enter and exit the soundstage while keeping the soundstage quiet. But choosing the right material for these giants can be tricky. As with the structure itself, elephant doors are best constructed of precast concrete, which require significant laydown space to pour and a crane to erect and install. Lifting a 16×16-foot concrete door into place on a tight site isn’t always plausible, unless you’re Layton Sr. Superintendent Dave Condreay.
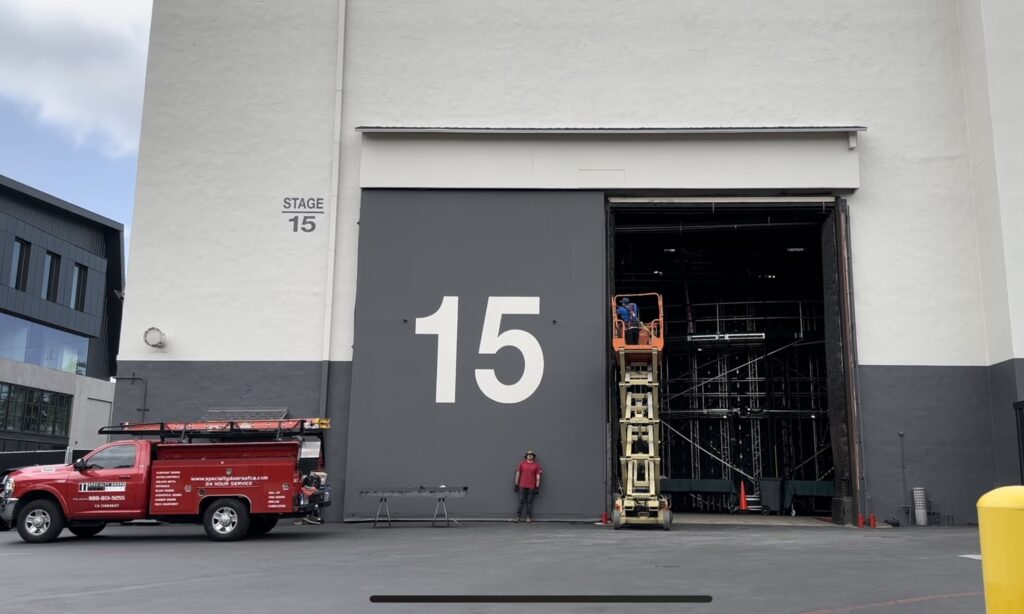
While working on a studio project for YouTube—set within an old aircraft hangar with no way to bring a crane in—Condreay came up with an alternative solution: shotcrete the doors. “It was a unique approach, but it saved time and costs since we didn’t use a crane or need to wait for the concrete to cure,” his brother Dan explains, adding, “It just goes to show the dichotomy in the industry with cost savings and acoustical ratings, and how to bring innovative solutions.”
Electrical Backbone: Cranking Things up to 11
Because a studio lot houses a myriad of functions, they not only need adequate power transmission but appropriate distribution. Studios utilize an array of equipment with varying power needs, from delicate cameras and monitors to powerful lighting rigs and sound systems. Layton must not only account for every connection point—and there can be thousands of them—but ensure they’re all tailored to the functions they’re powering. “Sufficient electrical infrastructure is as vital to a studio space as soundproofing,” says Thomas Smith, adding “it can be incredibly complex, similar to what you’d need for a hospital or mission critical facility.”
Studios utilize an array of equipment with varying power needs and all connection points must be accounted for.
Unfortunately, electrical details can be easily overlooked in the drawings, as has been experienced by the Condreay brothers in their studio experience, even with top companies. “We were looking at the drawings for a large studio, and Dave noticed the connection points in the catwalks were missing,” Dan explains, adding, “And I’ve seen the same thing for the star wagons. You need to look at where the connection points are and make sure you have the appropriate distribution.”
Star Wagons?
Interior equipment isn’t the only component that needs adequate power, or space. Outside is a similar story, as virtually any production studio needs the infrastructure to accommodate the star wagons—large, mobile trailers specifically designed to provide essential amenities and workspaces for cast and crew members while on location. “You always need a place for the trailers. It’s essentially a little compound outside the studio and it’s completely unique to the sector,” explains Condreay. And that’s the keyword through all of this: unique.
Studio Construction: In A League of Its Own
Yes, every market has its own challenges and unique elements. But perhaps only a few demand the considerations, relevant experience, and approach production studios do. The many moving parts, the permitting challenges, the site constraints, the everlasting need for flexibility and adaptability… Studios are a unique genre. And while nothing’s insurmountable, having a specialized team on board to provide insight, overcome obstacles, and assess each need is crucial. That’s where Layton shines. Given the similarities to industrial construction in how these spaces are built, coupled with seasoned studio experts who bring extensive hands-on experience, we’re well poised to bring these facilities to life.
See our California portfolio.
About Layton Construction
Layton Construction is a privately held national general contractor, delivering predictable outcomes in commercial construction since 1953. Headquartered in Salt Lake City, Utah, Layton operates from 16 strategic offices across the United States, employing more than 1,400 construction professionals who serve diverse markets including healthcare, education, commercial office, industrial, hospitality, and multi-unit residential. Founded on the core values of honesty, unity, safety, and quality, Layton has built a reputation for excellence in complex project delivery while maintaining strong partnerships with clients, architects, and trade partners nationwide.
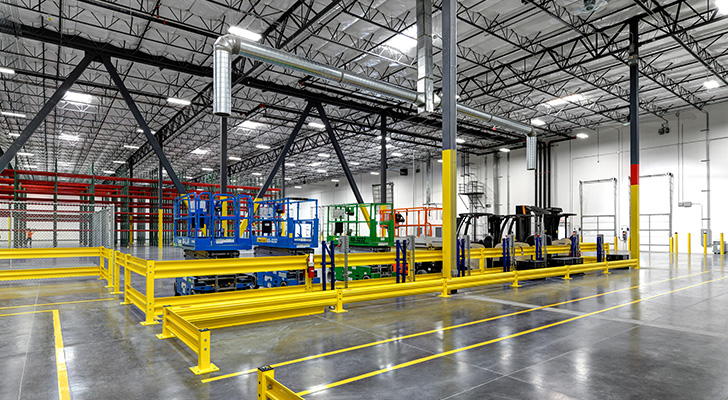
Considering the complexities of cold storage facilities, their construction demands a specialized approach and expertise. And with such a rapidly growing market, key players like Layton are primed and poised to step up.
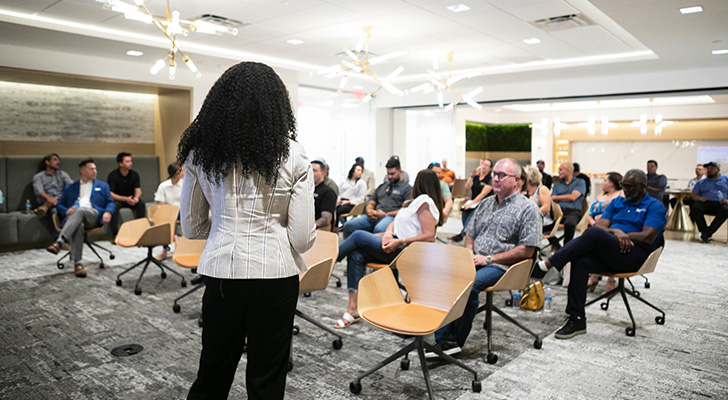
Layton depends heavily on the expertise and capabilities of our trade partners. Lead by Cherelle Cortez, our Trade Partner Engagement and Development team is focused on increasing the diversity and strength of our trade partners.