Kate Lyle brings over 16 years of architectural design expertise and is responsible for oversight of Ware Malcomb’s industrial cold storage and food processing practice across North America. She is active in the Controlled Environments Building Association (CEBA) and co-authored a cold storage e-book with NAIOP. Kate excels in planning, interpreting, organizing, and managing projects through all phases of development, including establishing and monitoring budgets, managing the project team, and preparing schedules to ensure efficient utilization of resources. She specializes in complex project types including food processing, manufacturing, and cold storage.
Do you see the speculative market growing in cold storage? Where do you see the trend of cold storage moving the next few years?
In the past, capital markets were unwilling to back cold storage, and construction funding was difficult to come by. At some point, people started believing this might be something to invest in. Once the money is there, then everyone is like: “Oh! This is exciting. How do we do this?” But it’s not simple.
We developed Cold Ready, in which you build a shell and install a cold storage solution customized to the end user, so we didn’t have the refrigeration systems at the front end of that. We hadn’t yet installed the slabs. We built it on column isolation blocks, but we didn’t necessarily put in all the systems on the first day. People discovered that it cost a lot less to make the initial investment and had a great fallback, but it took a long time to get those refrigeration systems, and those users wanted them sooner.
We decided to install refrigeration systems and began developing spec cold. Spec cold is the process of making a cold storage design building functional by multiple users. How do you take a building and create a refrigeration system and envelope that can cover a variety of cold storage users? We started building them and now have six across the country with dozens in the planning stages. It’s a growing market but still a tiny part of cold storage, which is a tiny part of industrial. So, it’s not the next big thing. It has the potential to be a viable method of building development.
It is a small market, but we’re also starting to see a lot of users looking to increase their capacity, several have said, “We have a growth pattern right now that is the biggest, we’ve ever seen.” Are you seeing that on your end too?
Yes, everyone wants more capacity. On the one hand, public refrigerated warehouses frequently lack space and are in expansion programs to build out more storage. Then there are the end users who do not want to rely on having external storage space if it is inconsistent, so what is the backup plan? They require at least some space in their buildings to store items. A cold storage component is becoming increasingly common in manufacturing facilities. The limitation of capacity is that people are landlocked.
We’re always asking ourselves, “How do we get the most bang for our buck?” What material handling systems can we employ to fit more pallets into a smaller space? How can we make more use of vertical structures? We always look at the existing footprint to see how people are making the best use of their space. Small changes can have a significant impact on people’s storage space.
How do you provide flexibility for your clients? They want something specific but don’t want to be locked into it forever. What solutions do you have?
We call it “future proofing.” You will be in a building and know what it will be for the next 10 years. But after that, what does it look like? What are the possibilities?
The need is constantly changing, as is the type of product. How do you design for flexibility? Is that a problem for speculative building?
Yes, there are ways to design buildings around refrigeration systems to have a temperature range. I’m looking for something that will take me from minus 10 to plus 35, right? That is a typical temperature range. The outside ranges become more challenging. Because a lot of produce is 55 degrees, following the specification doesn’t always make sense because there are fewer users. We’ve done produce markets, and that’s a different world, but for most buildings, it’ll make sense to have a plus 35 space that can be retrofitted later.
To meet the more specialized needs, you can close off a room and install a small refrigeration system. There are always specialty aspects of these buildings that must be done precisely for the end user. You want maximum flexibility, but so much of this is very specific, so how do you take something and say, “Okay, this is going to handle this specific need, but if you change this it would be something different. If you put in a different racking system or if you switch out your refrigeration system, there are ways that the building could still work.”
What advice would you give an owner who’s thinking about building a cold storage facility?
Choose the right team. You want to work with people who will advise you. Do your research. The Global Cold Chain Alliance (GCCA) has wonderful white papers available that can provide you with a lot of feedback on what and where design is going, which refrigerants to use, and what the regulatory requirements are. And consider the long term. Think about your building not just for today, but for the next 10, 20 years.
Where do you see the cold storage industry going in the next 5, 10, 20 years?
It’s constantly evolving. For example, when I first started out 11 years ago, the buzzword was farm to table, and consider how well-established that has become in our culture today. Huge changes have occurred over the years, all centered on the idea that we want our food fresher and from different sources. The way we get food has changed. The big thing now is e-commerce, and how we create cold storage for groceries that deliver directly to the end user. In the United States, no one has figured it out completely. Some things are looking up in Europe, and we’re starting to adopt some of them, but it’s still the wild west out there when it comes to cold storage for e-commerce. We’re always looking for creative ways to solve problems, and we’re seeing some interesting new developments. I’m paying close attention to the omni channel. How do you set up a store that can accept online orders? How do you move the retail environment closer to the industrial? We still treat them separately, but they’re getting closer.
Cold storage is constantly changing due to technological advancements. Refrigeration technologies and refrigerants continue to evolve. Another big thing right now is environmental and low global warming potential refrigerants. We made the switch to CO2 or ammonia a couple of years ago, but in smaller facilities, Freon still makes financial sense. As cap-and-trade systems are implemented, the EPA creates more regulations and it will no longer make financial sense, so we’re seeing a lot of spaces that I would never have thought would have CO2 or ammonia systems move in due to global warming concerns.
CO2 is gaining popularity, and people are realizing the environmental impacts and potential legislative impacts. It’s almost an added unnecessary expense put into the building to future proof it. What legislative and environmental requirements are presenting challenges not only for you as a designer, but also for the operators?
People like ammonia because it is an excellent refrigerant with low global warming potential. It is also extremely difficult from a regulatory standpoint. We began to see low charge ammonia, where we are minimizing the ammonia to lower thresholds, allowing you to avoid the regulatory nightmare.
Another big thing we’re seeing out here in California is warehouse moratoriums and everyone disliking trucks. Plus, no one wants to build any industrial, which is absurd in many ways, but it’s also a very real thing where every time I go to a planning commission meeting, someone stands up and says, “We need to think about the impacts that these trucks are having on our local environments.” As a result, we’re seeing more people consider future proofing by installing all the conduit and preparing for the truck charging stations that will be installed someday when the trucks arrive.
Regulatory environments are changing. Food safety is a major concern. The CDC can now perform extensive traceability of food pathogens. This has an impact on how we construct buildings. We want to make certain that all the facilities are kept clean.
I’m going to throw you a little curveball here: you have this cool porotype of drone deliveries coming in. Talking about what the future of cold storage looks like. How do you see technology and drone delivery impacting not only your design but our industry in general?
Drones are really fascinating. I think that there’s going to be a place for drones, certainly. The truck to drone systems they have going in some rural areas makes a huge amount of sense. You bring a centralized truck to an area and then you can do all the drones coming out of the trucks.
But that means you’ll need drone chargers and ways to get those drones off the truck in the back of your facility. Where will the drone be stored? How does one go about loading a drone?
We’re seeing drone pilot programs centered on pharmaceuticals, so that will play a significant role, especially as pharmaceuticals begin to shift toward more cold-required formulations, such as COVID-19 vaccines, which had to be ultra-low temperature. Drones make a lot of sense in life-saving situations where you need to get medicines across town quickly. They are typically small boxes that are light enough to be carried by a drone. When we consider pharmaceutical delivery or other integrated systems, we consider how to support that delivery in the future. As we transition to automated trucking and other systems, the world will change.
Up Next: Read More than a Warehouse: Building Cold Storageto learn more about Layton’s cold storage expertise.
Have questions about Layton’s cold storage experience? Or have a project coming up? Check out our portfolio and get in touch with our team to discuss.
About Layton Construction
Layton Construction is a privately held national general contractor, delivering predictable outcomes in commercial construction since 1953. Headquartered in Salt Lake City, Utah, Layton operates from 16 strategic offices across the United States, employing more than 1,400 construction professionals who serve diverse markets including healthcare, education, commercial office, industrial, hospitality, and multi-unit residential. Founded on the core values of honesty, unity, safety, and quality, Layton has built a reputation for excellence in complex project delivery while maintaining strong partnerships with clients, architects, and trade partners nationwide.
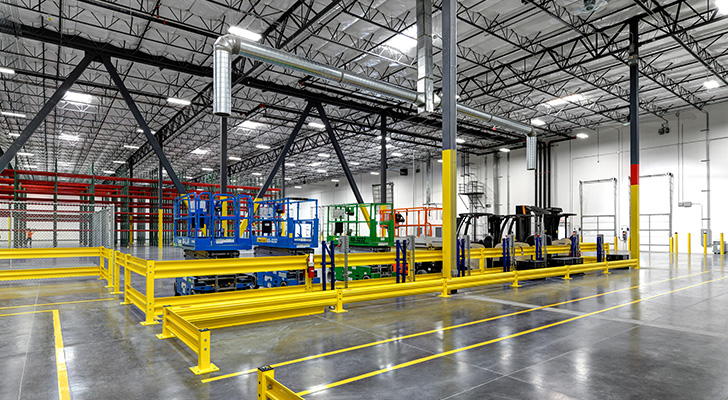
Considering the complexities of cold storage facilities, their construction demands a specialized approach and expertise. And with such a rapidly growing market, key players like Layton are primed and poised to step up.
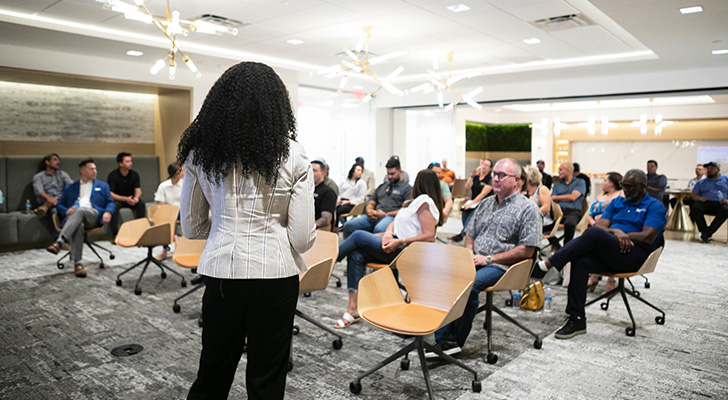
Layton depends heavily on the expertise and capabilities of our trade partners. Lead by Cherelle Cortez, our Trade Partner Engagement and Development team is focused on increasing the diversity and strength of our trade partners.